At Engaging Interiors Limited it is a time of change, we are starting to apply Circular Design Principles to our projects and it is making good business sense. The projects are more cost effective to build, quicker to construct and easier to adapt. One project that is a bit of a flag ship of how we want to work is the Zero Waste Shop at The University of Winchester. An important part of the interior fit out was a brand new product called Morph. Morph is a block system made from recycled plastic and can be recycled when no longer required. It can be built up in lego style to make partitions, desk bases or in our case a counter base. Following the successful specification and installation of the Morph system we thought it a good idea to interview its inventor to gain a greater understanding of how and why it came about. Harvey Banner is the man behind the block and talks us through this amazing new product.
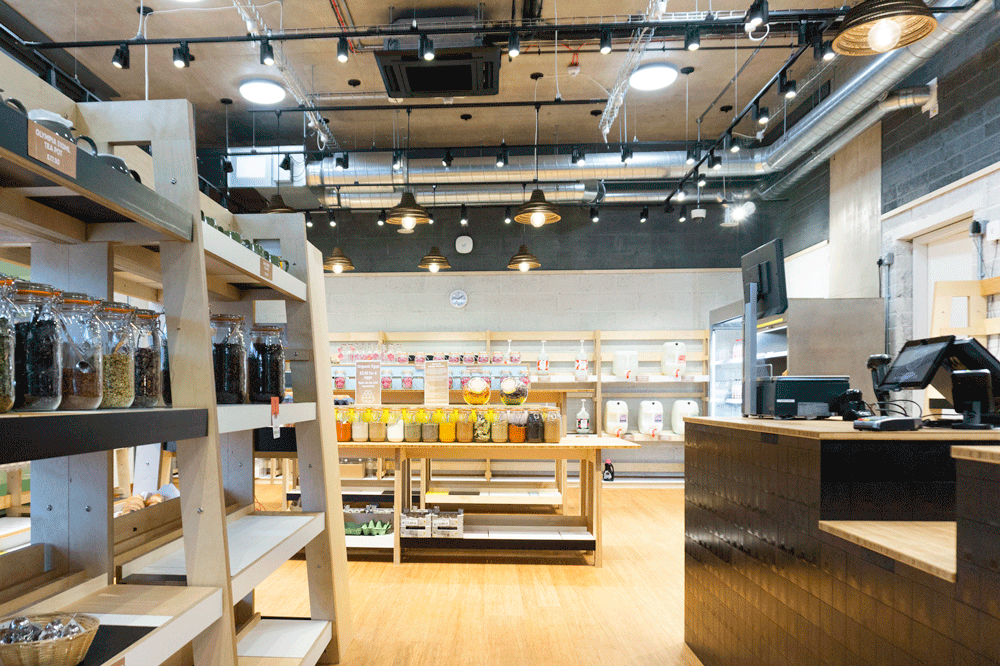
Interview with Harvey Banner | Creator of Morph
So Harvey, when was the light bulb moment with Morph and how long ago was it?
The idea started about 2 years ago when I was experimenting with different ways of recycling plastic. I realised that my efforts alone were not going to achieve a great deal and that I needed to develop a product that could re-use and raise the value of recycled plastic. Only then could I help increase interest in reclaiming plastic and tackle the improper disposal I was seeing and experiencing around me. I first started ‘playing’ with a 3D printer with some modular furniture ideas I have had over the years and the product developed relatively quickly from there. We raced through around 10 different variations in 2 weeks and soon refined the core components that make up Morph today.
Morph is made from recycled plastic and can be recycled after use, was this important and how hard was it to achieve?
The recycled aspect of the Morph project was critical. We decided at the start that if the product couldn’t use recycled raw material or be recycled then we wouldn’t proceed with the project. We were quickly able to use post industrial materials in the production process but our target was to use post consumer material. This took a little longer to achieve and some persuading to convince others that it was necessary, but we were able to persist with our aims and, by working with a local injection moulding company (Plastech), we have fulfilled our goal. As the material is 100% ABS then it is a simple process to rechip the material and remould it at a later date. And the very nature of the product enables it to be repurposed in its existing state, allowing the end user to keep on using blocks even when needs change – saving resources, challenging the throw-away culture in the furniture industry and supporting businesses to reduce their carbon footprint in the long-term. Walls could be deconstructed and re-built as desks for example. The opportunities are only limited by your own imagination.
One of the things we love about the product is that the scale of the blocks work really well with existing furniture standard dimensions. Were there any other sizes you considered or were the double blocks always going to be 150w x 75d x 75h?
We experimented with a few different sizes, always with the aim of having a unit size that would be easily expandable into dimensions commonly used in furniture or interiors. The 100mm base unit was strong but we had concerns over the cost implications for moulds as well as the unit feeling a little bulky and unrefined. The 50mm blocks were very neat but felt a little ‘toy’ like and we had concerns over the sheer volume of bricks that would be needed in larger structures. We settled on the 75mm core block size as it ticked all the boxes for the criteria we had set ourselves.
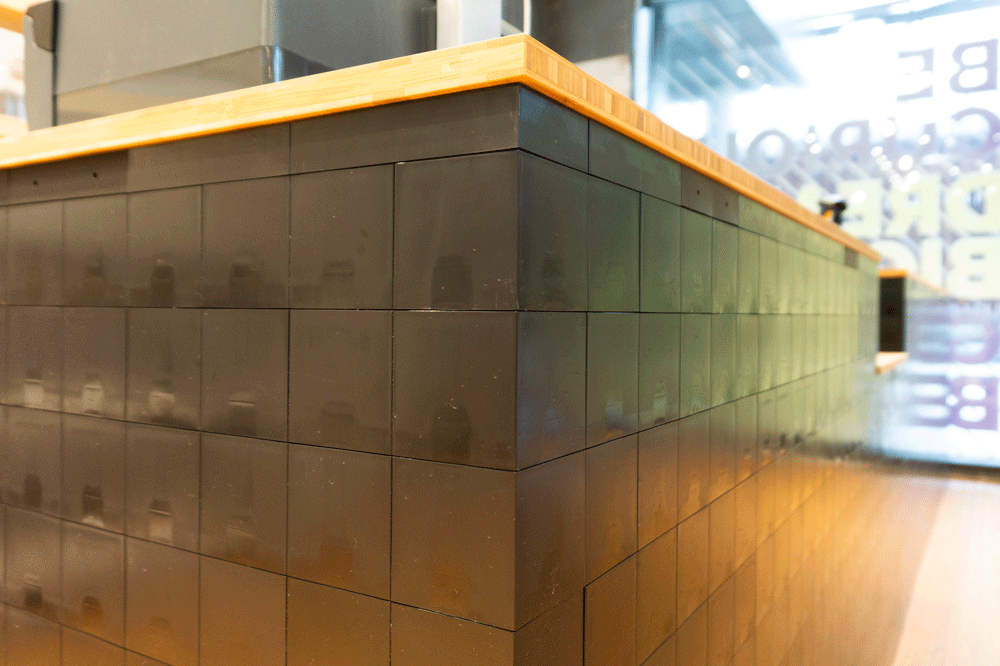
How much lego do you own?
I used to own a lot of Lego and I do encourage my kids to play with theirs as much as possible. Unfortunately, I’m not invited to join in with their builds as much as I would like. I do generally like to build and create things around the house and can easily get lost in a home DIY project.
Morph was designed initially to be installed into office environments, yet we have made a counter base out of it, what other opportunities are there for the little black blocks?
We wanted to start with the office Interior furniture and partitions as that is the market I am most familiar with. There are some fantastic opportunities in other markets though that we haven’t started to explore yet. Exhibition stands could be an excellent use for the product as well as possibilities with hire companies. We have been experimenting with @Giant Morph which are larger blocks built out of the smaller blocks that allow for very fast reconfigurations of products and repurposing. I think there are extensive opportunities here for schools. We could build stages out of the Giant Morph blocks which can be reconfigured into tiered seating, with lower stages or wide walls in a matter of minutes. Future iterations could even include emergency shelters or housing or outdoor offices and meeting pods. The opportunities are endless and a future aim would be to explore holding some design competitions with young designers at universities to see how they can use the system.
Do you have any plans to help interior designers / users build their own virtual Morph structures online?
Yes we are currently developing self build software to allow designers, architects and end users of all types to model their own constructions. The system will allow the basic structures to be built and then we can assist where necessary in finetuning the designs.
From a sustainability point of view what do you think will be the main challenges / opportunities for Morph as a product as it becomes more popular nationally and internationally?
As Morph becomes more popular we will need to monitor the supplies of the post consumer sources we are currently using. We are happy that the supply should remain consistent for a considerable amount of time, but we are also exploring other options. New materials are being developed all the time, some of which are carbon negative, giving us additional options for the future.
The international expansion of the product is something that we have been aware of from the start. Morph is a high volume product and we initially explored a flat packed version of the block for easy transport. However we decided against that and instead concentrated on creating a product where production is as simple as possible. Rather than transporting large volumes of product all over the world we envisage franchising the moulds to production centres in other countries. The product can be produced locally in this way, retaining its sustainable qualities.
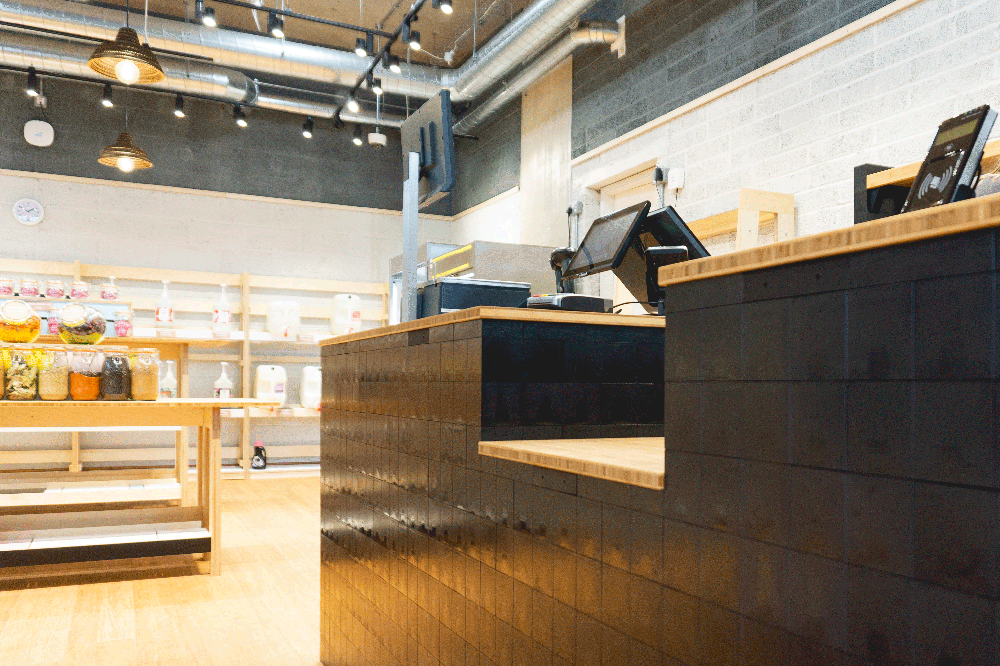
We loved how quickly you managed to install the front and back counter for the shop (3 hours) and we also were impressed by the accuracy of the block dimensions. How was it seeing the block system that was only an idea 24 months ago being installed into a working commercial environment?
The installation on the day was great fun. The various trades on site looked a little surprised that someone had turned up on their own to build both counters and was aiming to complete the work in just a few hours. As I started the build there was definitely some scepticism about the product I was working with, but very quickly various workers on site started engaging with the whole concept and working out how it could work well with their own trade. The electricians for example quickly worked out how to fix to the blocks and even used some additional blocks to build their own conduit.
The aim was always that the end result would be a geometrically predictable product that would allow worksurfaces to be fitted to the product quickly and easily. It was great to see this happen in practice though with the Six hands team arriving and dropping those lovely Bamboo shelves and tops into place. The contrast between the blocks and the Bamboo looked amazing too.